How To Repair Cracked Cylender
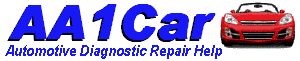
Home, Auto Repair Library, Auto Parts, Accessories, Tools, Manuals & Books, Car BLOG, Links, Index
Repairing Cracks
in Cast Fe Cylinder Heads and Engine Blocks
Copyright AA1Car Adapted from an commodity written by Larry Carley for Engine Architect magazine
Cleft repair has become one of today'south hottest topics because proficient rebuildable cylinder heads for many belatedly model engines are very expensive and hard to find. So many engine rebuilders are now repairing heads they would accept thrown out only a few years ago as unsalvageable.
In that location accept always been options for repairing cracks in cast atomic number 26. Pinning and furnace welding are both viable options that have long been used to repair cracks and other kinds of damage. But pinning has its limitations, and furnace welding is not something a novice can learn overnight.
Crack repair as well involves a sure corporeality of risk. That is why nearly of the crack repair action in the past was limited to high cost heavy-duty diesel heads, antique heads or other jobs that justified the time, effort and risk. But due to the high cost of many late model heads and blocks, crack repair may be a toll-effective alternative to buying a new or used casting to replace a cracked caput or cake.
OPTIONS FOR REPAIRING CRACKS
Cracks in aluminum heads and blocks are relatively easy to repair past TIG welding, but cast iron is much more difficult to weld. That is why pinning has long been the most popular method of repairing pocket-size cracks in cast iron blocks and heads. Pinning can repair nearly 80 per centum of all cracks just it tin can't fix every kind of crack. A lot depends on the location of the crack and its severity. Tapered pins with sealer work well on most applications. Welding, on the other mitt, restores integrity and allows you to fill cracks and holes. Yous tin even alter the shape of the combustion sleeping room or a port by calculation metallic.

Various types of pins can exist used to repair cracks
and holes in cast iron cylinder heads.
PINNING TO Set Cracked CYLINDER HEADS
Pinning is the nigh usually used technique for repairing cracks in cast iron head, blocks and manifolds considering it is fast, reliable and cheap. Pins tin can likewise be used to repair cracks in aluminum heads and blocks, too, although TIG welding is ofttimes the preferred repair method for aluminum. Pinning is a relatively easy technique to larn and employ, does not require much in the way of tools except a drill, guide fixture and tap, and uses no heat.

Overlapping pins seal the cleft.
Substantially, pinning involves drilling holes in a crack, installing overlapping pins to fill up the crevice, then peening over the pins to seal and alloy the surface.
At that place are two basic types of pins: straight and tapered. Each type has its advantages and may work improve in certain situations than the other.
Tapered pins pull themselves into a crack as they are tightened to provide a tight seal along the unabridged length of the pivot. This occurs considering the threads on both the tapered pin and pigsty have an interference fit. Sealer really is non necessary, only is often used for added insurance. The holes for tapered pins must be carefully paw tapped and the pins paw tightened for a tight seal.
Straight pins are faster to install because an ordinary tap and power drill can be used to install them. Directly pins are designed to twist off when tightened, eliminating the need to cut or grind the heads off (as is necessary with tapered pins). Straight pins also have an interference fit over their entire length, and a tapered shoulder that crushes into the surface. This eliminates a thread line on the surface enabling the surface to exist machined. This type of straight pivot can also eliminate the need for installing valve seat inserts in cast atomic number 26 heads.

Various types and sizes of crack repair pins and plugs.
Ordinary tapered and direct pins cannot handle certain kinds of cracks, such as those along an exterior edge or corner that require support to concord the sides of the cleft together. The same goes for cracks in an area of a casting that would open up up or pull apart when the casting is nether load or gets hot. For these types of scissure repairs, locking devices and/or pins with a cocky-gripping ability can provide the required reinforcement and strength. "Castmaster" pins (manufactured by Lock-Due north-Stitch) accept a unique "spiral hook" or "reverse pitch" thread pattern that grips both sides of a crack when the top shoulder of the pin bottoms against the metal. This blazon of pin can really concur a scissure together rather than simply fill it, and may be used to repair cracks that cannot be fixed with ordinary tapered or straight pins.
Another crack that is difficult to repair by pinning is whatever crack that occurs in very thin (less than i/eight inch wall thickness) expanse of a casting. Pins will non concur unless in that location is enough metal to grip and back up the threads.

Furnace welding uses a torch, an oven and lots of rut.
FURNACE WELDING Bandage IRON
Cracks in cast iron tin exist repaired by hot welding (furnace welding), only it is a technique that takes skill and lots of practice. It also requires preheating the casting earlier it is welded, and lots of heat (preheat to 1200 to 1400 degrees F. in n oven). The casting must as well exist ho-hum cooled seven to viii hours after welding to foreclose it from recracking.
Successful crack repair by furnace welding (hot welding) requires careful preparation of the fissure beforehand, and conscientious heat direction. Y'all cannot simply heat upwards a head with a weed burner. The right way is to preheat the head in an enclosed furnace or oven so the heat comes upwardly through the caput from the bottom. You have to keep the head insulated with a blanket and forestall any drafts while welding it otherwise you volition get cracking and porosity in the weld. The caput then exist slow-cooled afterwards.
When the head preheat temperature has stabilized (it takes about an 60 minutes), a "neutral flame" oxyacetylene torch with slightly more acetylene than oxygen is used to melt the cast iron (which melts at 2400 to 2600 degrees F). Bandage iron filler rod and borax flux and so used to fill the crevice. The trick is to keep the weld make clean by calculation a little flux and then the impurities will rise to the summit. The impurities can so be floated out of the repair expanse with the torch.
If a valve seat is being furnace welded, one play a trick on is to fill the hole with a graphite plug, then weld up around it. The puddle will be nearly half an inch deep and maybe two inches in bore. It takes a lot of rut to practice this, about 5000 degrees.
Later the crack has been filled comes a long, slow cool downwardly. If cast iron cools likewise quickly, one of ii things can happen. The surrounding metal can shrink away from the weld causing new cracks to open, and/or the carbon in the iron can turn to carbide making the metal also hard and brittle to machine. The casting must therefore be cooled very slowly to prevent these undesirable metallurgical changes.
Wrap the head in an insulating blanket and keep it in a hot box and then it volition cool at a rate of no more than 100 to 200 degrees per hour. The absurd down period can take up to eight hours. Later the head has cooled, information technology can be cleaned to remove the scale, then crude machined and submersion pressure tested in hot water at 100 psi to cheque for leaks.
If a cast fe caput has integral valve seats, replacing the exhaust valve seats after furnace welding is recommended considering the high temperatures of the process can destroy the induction hardening of the seats.
SPRAY WELDING CAST Fe
Another culling for repairing cracks in bandage iron heads and blocks is pulverization welding (too called flame spray welding). The basic technique has been around for many years but has been improved in recent years with new spray welding equipment. It can brand a strong a repair similar to hot welding but with much less heat. You still have to preheat and postheat the head to relieve stress that could cause it to recrack. Just with this technique, there is less take a chance of warping or distorting the head from excessive estrus.
Flame-spray welding requires a special oxyacetylene torch with a trigger-operated hopper that feeds nickel alloy powder into the flame. When the powder is exposed to the flame, it melts and fuses to the sides of the crack to fill the repair area. The procedure requires preheating the caput to about 700 degrees, and postal service-heating the head after welding to relieve stress.
The nickel alloy pulverization used for flame spray welding provides a hardness of eighteen to 22 Rc. Harder alloys are available for spray welding valve seats, camshafts and crankshafts.
As with any repair procedure, at that place is always a risk of recracking whether a casting has been repaired past TIG welding, furnace welding, spray welding or pinning. Cracks in the valve seat area may reopen if a new valve seat is pressed in with as well much interference fit. Welded areas on bandage iron may be harder than the base metal, making the casting more difficult to machine.

TROUBLESHOOTING FLAME-SPRAY PROBLEMS
If y'all are having problem achieving good results with flame-spray welding, here are some hints that may meliorate your success:
- If the nickel powder but lays there or stacks upward instead of wetting out when starting a weld, the work is too cold. The chamfer must be a dull ruddy red, or about 1300 to 1400 degrees F. Trying to force the base metal up to temperature by heating it though a thick .020 inch or greater layer of unfused pulverization will likely burn the flux out of the pulverization.
- If the nickel pulverisation boils upwardly when starting a weld and you get a volcanic like reaction when the initial burst of powder is sprayed into the chamfer, the work is besides hot. Back off the torch, allow the surface area to cool to a dull cherry red color, then concur the tip of the blue cone in the flame near 1/8 to one/2-inch from the deposit and add together fresh powder in short bursts. This should add plenty new flux to wet out the powder properly. If this does not work, cease, scrape the chamfer clean and outset over.
- If too much pulverisation is practical during the initial spray, it won't wet out. When unfused pulverization builds upward to .020 inch or thicker, it acts like an insulator between the flame and base metal. End, scrape away the unfused pulverization, and start over.
- Improper flame angle can also crusade the pulverization to ball upward and not wet out. If the flame angle is less than 75 degrees, powder can blow ahead of the puddle and stick to the chamfers. When unfused pulverisation stacks up to virtually .020 in. or thicker, it will not wet out properly. Trying to strength it out with the torch volition create porosity and hardness problems. Stop, scrape or brush away the unfused pulverization, hold the torch at the proper angle and start welding once again.
- Porosity and hardness bug in the weld can be acquired past surface contamination adjacent to the "V" chamfer. On some castings, manifolds in particular, the surface may contain a lot of "burned" iron. This should be ground away leaving sound, clean metal at to the lowest degree 3.viii to ane/2 inch on either side of the "V" chamfer. Rusty, dirty or burned metallic will mostly pop and crack when a flame is practical to information technology.
BRAZE WELDING CRACKS IN CAST IRON HEADS
Affix welding is yet some other pick for repairing bandage iron. It works bang-up on applications such every bit damaged bolt holes and even cracks in head ports because it is a simpler process. Braze welding can exist done at 800 to 900 degrees, which means the casting only heats up to about 400 to 500 degrees and does not distort or melt. Information technology works well for repairing cracks on the tops of thinwall cylinder heads, such equally Ford ii.9L heads, and tin can fifty-fifty be used to repair minor cracks in exhaust ports.
Related Manufactures:
How to Weld AluminumRelated Links:
Crack Repairs Methods Explained by Larry Carley Click Here to See More Carley Automotive Technical Articles
Exist sure to visit our other websites:
Carley Automotive Software
OBD2HELP
Random-Misfire
ScanToolCompanion
ScanToolHelp
TROUBLE-CODES
Source: https://www.aa1car.com/library/ar497c.htm
Posted by: jonesmrse1992.blogspot.com
0 Response to "How To Repair Cracked Cylender"
Post a Comment